The Lotus Emira will roll out from the newly opened Chapman Production Center
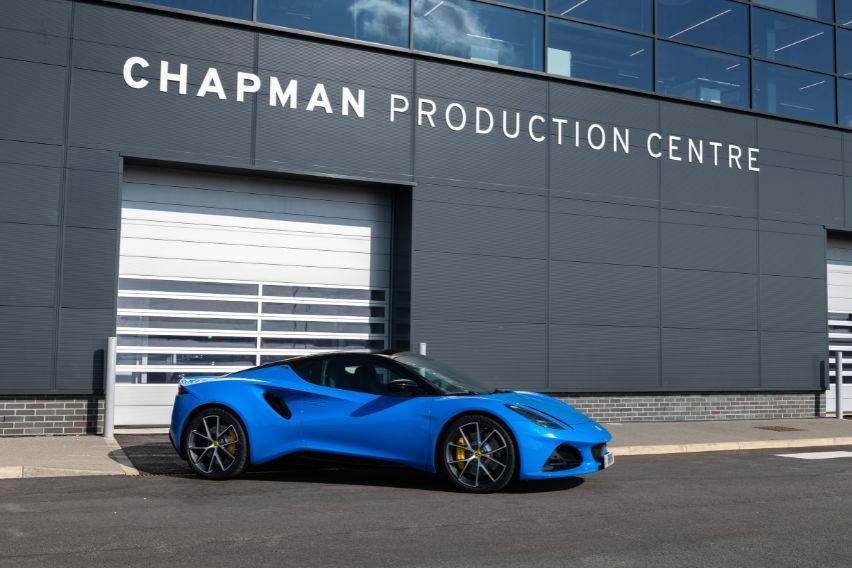
MANILA: Lotus has dedicated its new sports car manufacturing site in Hethel, England to the company's founder and inspiration, Colin Chapman.
KEY TAKEAWAYS
How many vehicles can the Chapman Production Center produce annually?
The Chapman Production Center has a capacity of 5,000 vehicles per year.What are the key features of the Chapman Production Center?
The facility has a new paint shop that uses automation to apply primer, color, and clearcoat. It also uses the new Lotus system which is extremely energy efficient: dry filtering consumes 60% less energy than wet filtration, and an electrostatic primer on body panels will cut paint usage by 30% to 40% compared to the traditional hand-sprayed method. Due to a partnership with energy supplier Centrica, the facility is powered entirely by renewable electricity.The Chapman Production Center is a world-class center of excellence that is already manufacturing the Emira, Lotus' last petrol-powered model.
Lotus Cars Managing Director Matt Windle and Classic Team Lotus Managing Director Clive Chapman led the opening ceremony. Several hundred Lotus employees were also in attendance.
The Chapman Production Center, along with Lotus Advanced Structures (LAS), is part of Lotus' £100-million investment in the UK. It is also an investment in the abilities and commitment of the Lotus team, which has more than doubled since Geely became the main shareholder in 2017.
Lotus has hired additional personnel across the board, including skilled production workers, engineers, and technicians. The company has added 300 new employees to its vehicle assembly and production operations. All recruits have been trained in the high-quality production processes they need to start their career at Lotus through the new Lotus Learning Academy, which is located at LAS.
During the ceremony, Windle said, “Lotus is transforming from a UK sports car company to a truly global performance car business and brand, and the new Chapman Production Center is a symbol of us delivering on that ambition. We are proud of our past successes and excited about our all-electric future, which was started all those years ago by our founder Colin Chapman, and I am honored that Clive and Jane could join us to mark this occasion.”
Meanwhile, Chapman stated, “I am honored to have been part of this significant day in the history of Lotus. For the Chapman family it is extraordinary to witness Lotus on the path to becoming a global car manufacturer. I am delighted to have this opportunity to wish every success to all those who will be working in the Chapman Production Center, and to thank Geely and Lotus for honoring Hazel and Colin in such a splendid manner.”
The new Chapman Production Center, which has a capacity of 5,000 vehicles per year, is one of the world's most modern low-volume automotive production plants. The new paint shop is a cutting-edge facility that uses automation to apply primer, color, and clearcoat, resulting in an extraordinarily high-quality finish, rapid vehicle turnaround, and precise reproducibility. The new Lotus system is extremely energy efficient: dry filtering consumes 60% less energy than wet filtration, and an electrostatic primer on body panels will cut paint usage by 30% to 40% compared to the traditional hand-sprayed method. Due to a partnership with energy supplier Centrica, all Lotus sports car operations in Hethel and Norwich are powered entirely by renewable electricity.
The buildings that housed the previous Lotus assembly lines have now been transformed to sub-assembly. They currently contain the all-new framing line, which is responsible for building the car bodywork as part of Emira pre-production, with robots putting bonding agents to the sides, roof, and cantrails.
New Automated Guided Vehicles (AGVs) provide very efficient movement of cars-in-build on set routes across the facility, letting operations teams concentrate on vehicle assembly. Lotus has future-proofed its sports car production system by incorporating AGVs, which allow for rapid and easy alterations to adapt new manufacturing procedures as new vehicle models are released.
The main assembly line is also equipped with Wheel Alignment and Headlamp Aim (WAHA) equipment, a Vehicle Configuration and Test System (VCaTS), a monsoon water test booth, a rolling road, and a fuel fill area.
Located near the Chapman Production Center is a new validation track where all production cars are tested as part of the quality assurance process. This dynamic test facility is an essential part of the vehicle sign-off procedure, one of many that guarantees the highest quality.
Photos from Lotus Cars
Also read: WATCH: Lotus unveils first EV and SUV, the Eletre
Sell your car at the best price


Lotus Car Models
PIMS 2024
- Latest
- Popular
You might also be interested in
- News
- Featured Stories
- Latest
- Popular
Latest Lotus Car Videos on Zigwheels

Lotus Car Articles From Carmudi
- journal