Volkswagen opens Battery Engineering Lab in Tennessee
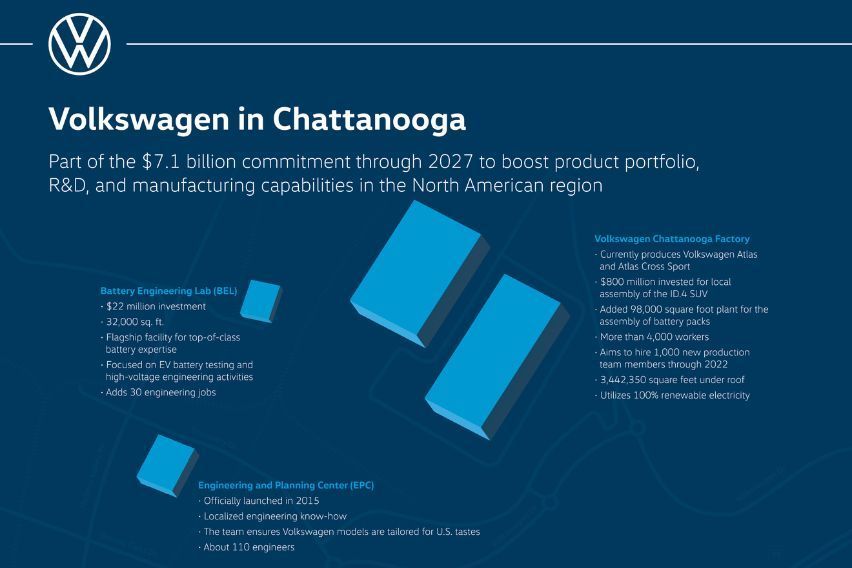
MANILA: Volkswagen of America (VWoA) has announced the opening of its Battery Engineering Lab (BEL) in Chattanooga, Tennessee, which will test and develop batteries for all electric vehicles (EV) sold in the American market.
KEY TAKEAWAYS
What activities will be done at Volkswagen's Battery Engineering Lab (BEL) in Chattanooga, Tennessee?
The new BEL will focus on EV battery testing and high-voltage engineering activities.What are the highly specialized equipment installed at the new BEL?
The laboratory is equipped with an electrical Multi-Axial Shaker Table, drive-in climate chamber, thermal shock chambers, and water immersion tanks.By developing key battery expertise in-house at the US$22-million, 32,000-square-feet facility, Volkswagen will gain an advantage in the transition to electric mobility. The BEL is the latest development in Volkswagen's US$7.1-billion commitment to expand its product line, research and development, and production capabilities in the North American region. The ID. 4 compact SUV, the first Volkswagen EV manufactured in America, is set to hit the streets this year.
In a statement, Volkswagen Group of America, Inc. President and Chief Executive Officer Scott Keogh said, “When we began making investments in electrification, it was because we saw a future for our industry and the North American region in which Volkswagen could take a leadership position. The Battery Engineering Lab helps make that vision a reality today, accelerating us decades into the future with advanced battery engineering to support our expanding EV push in North America.”
The BEL is VWoA's first facility of its kind, and one of four strategically located Volkswagen Group units worldwide, with one in Germany (Braunschweig), and two in China (Shanghai and Changchun). Engineers will first concentrate on batteries and battery packs for Volkswagen's MEB vehicle platform, with the possibility of including various types for all Volkswagen Group brands.
Volkswagen plans to explore potential battery technologies in the future and gain an early insight of how new concepts and prototypes can endure the company's stringent standards. These findings are essential as battery technologies develop in terms of energy density, weight, and cost, influencing the characteristics of EVs.
“We are applying cutting-edge technologies to make sure that our EV batteries and ultimately our electric vehicles for American consumers are safe and strong. With our new Battery Engineering Lab as the new center for battery know-how, we can react quickly to the fast-paced EV market by applying data to our local engineering and assembly,” VWoA Executive Vice President and Chief Engineering Officer Wolfgang Demmelbauer-Ebner stated.
Over 100 engineers from VWoA's local engineering department in Chattanooga work on everything from chassis to driving performance, interiors, and digital technologies. Volkswagen is introducing more highly qualified positions with the BEL. A new team of 30 engineers will concentrate on various climatic, mechanical, electrical, and corrosion tests of battery cells and battery packs, either on-site or remotely via cloud access. They can simulate every climate in the world and scale between extreme settings much beyond what a typical customer would subject a vehicle to. This is especially relevant in countries like the United States, and even more so in the North American continent, which has a wide range of climates, from arctic cold to desert heat.
Volkswagen was able to install highly specialized equipment because the BEL was built from the ground up. The electrical Multi-Axial Shaker Table (eMAST) is one of them. This one-of-a-kind machine can do intense vibration tests to simulate one average year of driving in just one week. Other primary tests include a drive-in climate chamber that can accommodate a larger SUV model and the ability to set temperature ranges between -70 degrees and 130 degrees Celsius to mimic hundreds of possible climate conditions.
The BEL also has thermal shock chambers that quickly expose battery packs to varying hot and cold environments to strain their welds and fasteners, durability tests with certified, super-fine "Arizona" dust to add abrasive elements and test the sealing of battery packs, and water immersion tanks to recreate water ingress scenarios.
The BEL's commitment to sustainability extends beyond its work to the facility's operations. When the batteries are discharged during testing, the energy is returned to the building, and the scrapped materials and local public grid are recycled.
Volkswagen has invested more than US$800 million in its Chattanooga plant to ready it for local production of the ID.4 SUV in 2022, including dedicated vehicle and battery pack assembly facilities. The ID. product line-up and battery packs use an unified modular approach based on the global Volkswagen Group's MEB electric vehicle platform. Volkswagen has already transformed four of its global plants to produce these MEB-specific battery packs, with sites in Germany, the Czech Republic, and two in China. Volkswagen employs around 4,000 people at its factory, with plans to hire 1,000 new production team members by 2022 to help meet customer demand for the Atlas, Atlas Cross Sport, and upcoming ID. 4.
Photos from Volkswagen of America
Also read: Volkswagen begins production of ID. Buzz in Hannover, Germany
Sell your car at the best price


Volkswagen Car Models
PIMS 2024
Trending & Fresh Updates
- Latest
- Popular
You might also be interested in
- News
- Featured Stories
Volkswagen Featured Cars
- Popular
Latest Volkswagen Car Videos on Zigwheels

Volkswagen Car Articles From Carmudi
- journal