BMW Group to 'substantially' cut CO2 emissions through use of low-carbon steel
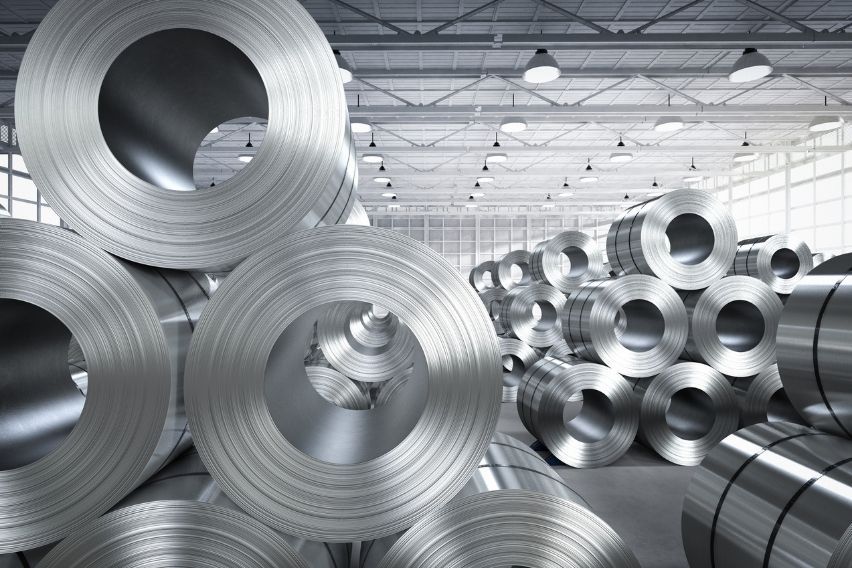
MANILA: As part of its ongoing sustainability efforts, the BMW Group continues to minimize CO2 emissions throughout its supplier network. This is made possible in part by using steel produced from natural gas or hydrogen, instead of fossil resources like coal. The BMW Group has now inked a corresponding deal with Salzgitter AG for the delivery of low-carbon steel. The steel will be used in standard production cars at the BMW Group’s European plants from 2026 onwards. BMW now has two suppliers for low-carbon steel. The use of low-carbon steel aims to meet over 40% of demand at the company’s European plants by 2030, thereby cutting down CO2 emissions by up to 400,000 tons per year.
KEY TAKEAWAYS
What occurs in the closed-loop material cycle that the BMW Group and Salzgitter AG developed more than five years ago?
After the delivery of steel coils to the plant, Salzgitter AG takes away steel fragments created at press plants, such as when doors are punched out, and recycles the material to make new steel. The BMW Group plants then get this steel. In this approach, raw material can be reused several times in a circular economy, helping save natural resources.How many tons of steel are processed in the BMW Group's press plants every year?
More than half a million tons of steel are processed in the BMW Group’s press plants yearly.In a statement, BMW AG Board of Management for Purchasing and Supplier Network Member Joachim Post said, “This is an important step in substantially reducing CO2 emissions at source in the supplier network. Our aim is to reduce vehicles’ lifecycle carbon footprint with a holistic approach. With steel, in particular, we are leading the way by sourcing low-carbon steel for our plants in Europe in the future.”
From 2025 onwards, the BMW Group will use steel made using hydrogen and green power from northern Sweden, reducing CO2 emissions by up to 95%. More than half a million tons of steel are processed in the BMW Group’s press plants every year.
Because of its energy-intensive process, steel production produces a lot of CO2. Steel is one of the most significant materials for car production, and it will continue to account for a large proportion of the body and compartments due to its versatility.
Salzgitter AG is gradually transitioning to virtually carbon-free production in order to reduce CO2 emissions from steel production on a large scale. The use of renewable energy in the production of hydrogen by electrolysis is a key component of the transition. This green hydrogen will take the place of the coal that is currently used in the blast-furnace process. Direct reduction plants, which employ hydrogen to directly reduce iron ore to iron in the solid state, make this possible. The solid iron is then melted down with steel scrap in an electric arc furnace driven by renewable energy.
Salzgitter AG plans to employ this approach to cut CO2 emissions from steel production to 5% of what they were previously were.
More than five years ago, the BMW Group and Salzgitter AG created a closed-loop material cycle for sheet steel scrap from BMW Group Plant Leipzig. After the delivery of steel coils to the plant, Salzgitter AG takes away steel fragments created at press plants, such as when doors are punched out, and recycles the material to make new steel. The BMW Group plants then get this steel. In this approach, raw material can be reused several times in a circular economy, helping save natural resources.
Sheet steel waste from the BMW Group’s other European plants is either reused or transported back to the steel manufacturer via steel traders to be processed into new steel.
Recycling loops already account for up to a quarter of the steel used in BMW Group vehicles. The group intends to increase its use of secondary steel in stages, reaching up to 50% by 2030.
CO2 emissions from secondary steel production are, on average, 50% to 80% lower than primary steel production because it uses much less energy.
In addition to procuring low-carbon steel, the BMW Group has invested in an innovative process for carbon-free steel production created by American startup Boston Metal. With the use of an electrolysis cell, Boston Metal’s breakthrough technology produces molten iron, which is then processed into steel. If electricity from renewable sources is applied in this process, then steel production is carbon-free. Boston Metal hopes to extend the new method of steel production on an industrial scale in the next years.
By investing in startups, the BMW Group strives to expedite new technology development, stimulate competition, and offer incentive that will make it easier for fledgling enterprises to enter the market. New technologies make access to raw materials more sustainable and more efficient.
Investing in new technology is one of the many efforts done by the BMW Group to reach its ambitious goals for the steel supply chain, such as making low-carbon production a major award criterion for every contract.
Photos from BMW Group
Also read: BMW's Spartanburg plant establishes new record with 443,810 X units made in 2021
Sell your car at the best price


BMW Car Models
PIMS 2024
Trending & Fresh Updates
- Latest
- Popular
You might also be interested in
- News
- Featured Stories
BMW Featured Cars
- Latest
- Popular
Latest BMW Car Videos on Zigwheels

BMW Car Articles From Carmudi
- journal