Hyundai's cutting-edge VR technology makes car design process more sustainable
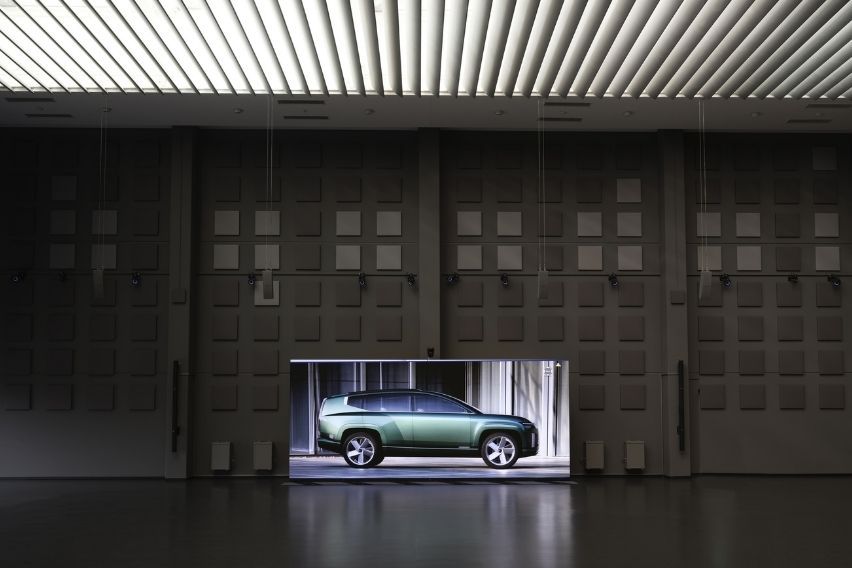
MANILA: Hyundai Motor has invested in a number of cutting-edge technologies to improve its design process in recent years. The company has solidified its place at the vanguard of automobile design by adopting the latest innovations, such as virtual reality (VR) and 3D gravity sketching.
KEY TAKEAWAYS
What are the advantages of Hyundai's latest innovations?
Hyundai designers now have access to cutting-edge tools that allow the company to create cars with groundbreaking features. Furthermore, a streamlined digital procedure accelerates the creation of vehicles. Finally, a smaller carbon footprint helps the company meet its environmental goals.What is Seven?
Seven is Hyundai's first fully digitally designed vehicle.The advantages of this approach are three-fold, in addition to pure aesthetics. To begin with, Hyundai designers have access to cutting-edge tools that allow them to create cars with groundbreaking features. Furthermore, a streamlined digital procedure accelerates the creation of vehicles. Finally, a smaller carbon footprint helps the company meet its environmental goals.
Hyundai designers start the creative process with pencil sketches on paper. These illustrations portray the type of car they intend to show, such as one that is dynamic and sporty or one that is loaded with cutting-edge technology. These sketches usually feature exaggerated proportions of the car, such as over-emphasized wheels and curves.
Designers would compete with one another after finishing their first sketches in order to have their proposals chosen. After the selection of a winning design, the chosen model would be created as a scale model out of clay, based on two-dimensional paper sketches.
Depending on the schedule, creating a scale model could take anywhere from four weeks to two months. After that, the scale model would be scanned and machined in full scale. However, there are several disadvantages to this strategy. After all, no line remains the same while going from a scale model to a full-size model.
Previously, Hyundai designers had to collaborate with clay modelers to fine-tune an upcoming model's final design. Lines and surfaces, on the other hand, have to be traced out using tape. Furthermore, Hyundai engineers were unable to work with the designers at the same time because data could only be obtained once the model was scanned with a photogrammetry system. Both of these factors contributed to the process taking a long time and costing a lot of money.
In recent years, Hyundai's design approach has seen a transformation. Hyundai designers now have access to a variety of cutting-edge tools. Before delving into some of these, it is worth noting that the first sketching stage — and the ensuing battle between different design teams to have their proposal chosen — is still crucial to the development of the initial vision for a new Hyundai model.
“If you're scared of doing something new, don't work in design,” Hyundai Motor Company Styling Head Simon Loasby stated. In 2017, Loasby was appointed Director of Hyundai Design in China. He was a key figure in establishing Hyundai's design identity in the country. Currently based at HMC's global R&D and Design Center in Namyang, Korea, he has played a big part in integrating Sensuous Sportiness into the company's BEV-dedicated Ioniq lineup, including Ioniq 5 and Hyundai's latest concept, Seven.
“Design is about not being fearful of getting it wrong sometimes — 99.9% of what a designer does goes in the bin. I have a presentation which is called ‘Rubbish’, because the rubbish bin is something that has to become your friend as a designer. You have to expect that lots of your work will eventually go there: unfortunately, 99.9% of the design work we undertake lands in the bin. Our job is to explore and to find that amazing remaining 0.1%. We have to be comfortable with getting things wrong, and we have to encourage our teams that it's okay to get it wrong. If you don't try going down there, you never know what's at the end of the path you're creating,” Loasby added.
Modern design technology is significantly faster and more reliable than before. Hyundai no longer makes scale clay models. Instead, it uses technologically advanced tools that are more intuitive, such as 3D digital design software. Hyundai engineers can now mill full-scale models using 3D data, considerably speeding up the design process. Eighty percent of the company's design development is now fully digital.
Hyundai designers use modified industry-standard software that allows them to collaborate across multi-user and multi-location setups. This technology includes laptops intended for high-performance gaming in order to handle 3D graphics, motion technologies from the film industry, and technologies inspired by sport. Designers can use this program to create models and immersive virtual reality environments that are incredibly realistic. The contrast between current design and old approaches is striking, and can be compared to the transformation that automobiles underwent before and after anti-lock braking systems were incorporated.
For Hyundai designers, virtual reality technology brings up a slew of new possibilities. The gravity sketching tool, for example, makes it possible to develop more human-centric vehicle designs by working in 3D from the start. Designers trade in their pencils and paper for a headset and controllers to immerse themselves in virtual reality, replicating gestural interactions using motion tracking. Hyundai designers may play with various dimensions and create alternatives based on their ideas because they work in 3D. In contrast to the usual 2D method, a 360-degree view of the car allows them to sketch from any angle.
The coordination between Hyundai's exterior and interior designers is supported by 3D gravity sketching. The two teams can work concurrently, thanks to this technology. While the exterior design team refines the digital model, the interior design team can work simultaneously by virtually going inside the vehicle to build features or make quick alterations.
Hyundai designers may also test a limitless number of color options and material applications, such as textiles and leather, ambient lighting, and other types of materials with the help of this technology. This saves time while also lowering shipping costs. Furthermore, this process is far more sustainable because it produces significantly less waste, resulting in a large reduction in CO2 emissions.
Hyundai began developing multi-user wireless VR spaces in 2017. Hyundai Motor Company and Kia Motors Corporation then launched a major new VR design evaluation system in December 2019. This has now been fully utilized for two years. The system displays a greater emphasis on using VR technology to improve car development processes.
These state-of-the-art facilities in Namyang, Russelsheim, and Irvine, California, enable designers to evaluate a wide range of design concepts earlier in the development process and in ways that were previously unimaginable.
These changes have officially begun before the COVID-19 pandemic put the world on lockdown in early 2020. According to Hyundai's global design staff, the pandemic played a pivotal role, hastening the shift to digitalization and agile working.
“When our studios across the world were sending all the designers home, we were fortunate that we were already operating a very well-oiled machine in terms of remote virtual connection, where we could all connect across three different continents and five different locations into a virtual working space and walk around the cars,” Loasby said.
Hyundai introduced the Seven concept, the first fully digitally designed vehicle, at the 2021 AutoMobility LA. The company's Electric-Global Modular Platform (E-GMP) is used to create its expansive exterior design. Meanwhile, the interior architecture provides passengers with more freedom and comfort. It gives a luxury lounge experience with furniture-like seating and hygienically focused features.
“During the pandemic, our Seven concept really benefited from this virtual process. When we completed the digital design sign-off of the car, Luc Donckerwolke, SangYup Lee, and I were all in completely different locations, while our European team were in the discussion, too. We were in the same virtual location looking at the model, and did a complete virtual sign off of the whole car: both exterior and interior. Remarkably, I hadn’t seen the physical model at that point, which must be a world-first for a lead automotive designer,” Loasby added.
Hyundai's technological innovation is further evidenced by a small portmanteau created specifically for Loasby by the company's digital team. Loasby is so impressed by the device that he fondly refers to it as his "James Bond suitcase," a reference to the legendary cinematic spy. He recently discussed it on Hyundai's "Are We There Yet?" podcast.
Loasby's "James Bond suitcase," shaped like a travel bag, is packed with a laptop, VR goggles, cables, and handsets. He may carry it with him wherever he goes and when engaging in virtual design reviews with colleagues all over the world.
“I’m very fond of the carry-on bag I call my ‘James Bond suitcase’, because it ensures I can connect to our virtual conferencing space and conduct design reviews from anywhere, at any time. In fact, one of the craziest design reviews I did was at Incheon Airport. I was about to fly somewhere, but I needed to check in on the progress of a development quickly. So I took the gear out, plugged it in and set up my virtual studio next to Starbucks and conducted a review from the departure terminal,” Loasby shared.
Hyundai has also upgraded the 20x23m Vision Lab at the Hyundai Motor Europe Technical Center (HMETC). It was completed in November 2021. It is now equipped with some of the most cutting-edge design technologies in the industry, including 48 cameras with active tracking, highlighting Hyundai's shift to a Smart Mobility Solution Provider.
“Our new HMETC Vision Lab is a marvel in terms of infrastructure and technology. The combination of 3D software and VR goggles enables us to dive into a virtual environment, seeing the car in full size and 3D as if we were standing right next to a physical model. In this virtual 3D environment, we can also stand just one meter away from our Global Head of Design, who is based 10,000 kilometers away from the European studio. This means we’re able to freely exchange concepts within our global design organization and make much quicker developmental decisions and technical assessments from the very outset of a project,” Hyundai Europe Chief Designer Thomas Burkle stated.
The LED wall, which has an integrated 8K video system, is one of the significant upgrades to HMETC's Vision Lab. Up to eight streams can be presented on the screen at once, allowing those who are not wearing VR headsets to attend the virtual conference.
HMETC employees also have access to HP's cutting-edge goggles. These come with a clip from OptiTrack, a well-known motion tracking provider. The clip has eight trackers that produce light signals to the cameras. The goggles provide an extremely detailed picture of the design that is near to a real-world replication, with accuracy of one centimeter.
“In the Vision Lab, our designers are able to make adjustments to the digital model with much greater accuracy using not just VR, but also AR and mixed reality. They’re able to hone in on a bumper detail using digital laser pointers, for example, and can define lines and shapes more accurately and efficiently than in the past. The almost immediate visualization of design data can also be quickly shared with engineers at a very early stage of the project, so the designers get faster feedback for modifications. These levels of precision allow Hyundai to respond quickly and react with agility to the needs of our customers, as well as the paradigm shifts in the automotive industry,” Burkle said.
VR technology is still evolving. It will be able to provide far more details and functions at much faster speeds in the future. It is expected to play a bigger part in the work of Hyundai designers and engineers. Furthermore, improvements in augmented reality and mixed reality will allow Hyundai employees to communicate with one another even more immersively.
One important benefit that should not be neglected is its good impact on the environment. Because there is significantly less clay, paper, and waste materials needed in the digital design process, it produces a much lower carbon footprint. For instance, Hyundai built a single clay model for verification at the end of the development of Seven, rather than a slew of scale clay models. Hyundai designers are also no longer required to travel around the world on a regular basis, wasting thousands of air miles in the process, by convening in a virtual conference space. In the future, this will help Hyundai achieve its aim of becoming carbon-neutral by 2045.
Photos from Hyundai Motor Company
Also read: 2 Hyundai SUVs earn spots in Kelley Blue Book’s Best Family Cars of 2022
Sell your car at the best price


Hyundai Car Models
PIMS 2024
Trending & Fresh Updates
- Latest
- Popular
You might also be interested in
- News
- Featured Stories
Hyundai Featured Cars
- Latest
- Popular
Latest Hyundai Car Videos on Zigwheels

Hyundai Car Articles From Carmudi
- journal
- financing
- insurance