Geely showcases 1-car-per-minute Changxing factory
4th-gen Emgrand sedan built in Changxing factory
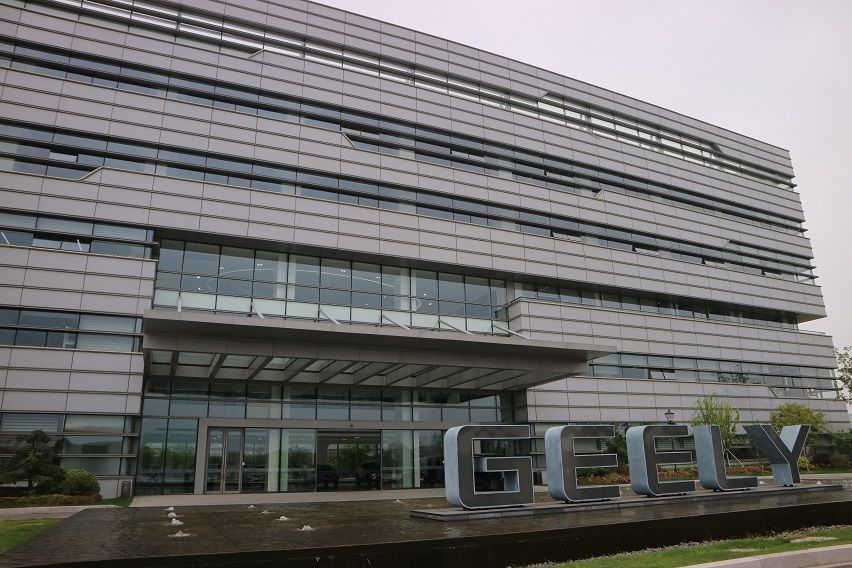
MANILA: Geely Auto has showcased its smart factory in China to select members of the Philippine motoring media.
KEY TAKEAWAYS
What are the four major assembly processes involved in the manufacturing system used in Geely’s Changxing factory?
The four major steps used by the Geely Changxing plant are high-precision stamping, automated welding, eco-friendly coating, and AI-powered assembly.What are some of the examples of inspection and quality testing procedures used in the said facility?
Per Geely, the factory subjects vehicles to track tests and weather tests.Zigwheels Philippines was part of the contingency that toured the Chinese carmaker’s plant in Changxing, which the marque noted can produce one car per minute.
Per Geely Auto, the fast and efficient production of cars in the aforementioned facility is due to the “advanced 5G connectivity” that links every point of manufacturing together to ensure efficient production while maintaining strict quality control.
Here are some of the steps that contribute to Geely Auto’s intelligent and automated plant in the island province of Dalian.
High-precision stamping
According to Geely Auto, the cars produced in its Changxing factory first undergo a high-precision stamping procedure.
The auto firm has two fully automatic stamping lines in its smart factory that cater to complex panels of the multiple models produced therein. These stamping machines — Geely Auto noted — boast production efficiency of up to 15 strokes per minute, which means one part can be produced in four seconds.
Every stamped part — the company added — is strictly inspected, with an error threshold of less than half a millimeter, which is less than the thickness of a strand of hair.
Automated welding line
The abovementioned stamped parts then head to Geely Auto’s welding shop, which is 100 percent automated.
Materials to be welded are transported to each workstation by many automated guided vehicle (AGV) robots controlled via the 5G network. After which, work is carried out by artificial intelligence (AI)-powered robots that perform some 4,600 welding spots per car.
The aforementioned robots use Arplas welding (to ensure that the connection spot is perfect and neat) and a three-dimensional glue detection system (for good air tightness of the car’s body).
Eco-friendly coating process
Once the stamped parts are welded, they next proceed to Geely Auto’s eco-friendly coating line.
The carmaker revealed that the coating process produces no metal emissions and fully complies with the local environmental protection regulations. Further, its coating shop has adopted high-penetration electrophoresis technology offered by top world-leading coating brands such as PPG and BASF.
On that note, the paint surfaces of the cars produced in this factory are extremely translucent, environmentally-friendly, and durable.
AI-powered assembly process
Geely Auto also uses AI technology for its assembly process. These robots achieve an accuracy rate of up to 0.1 millimeters. In addition, AI tightening systems were introduced to realize real-time monitoring of the tightening process and full traceability of tightening data.
A tightening application intelligently identifies and analyzes torque trends. Further, it provides early warning to ensure that the one-time tightening torque is 100 percent qualified.
Top-quality inspection system
Geely Auto prides itself in implementing a stringent, comprehensive, and high-standard quality inspection system.
Every vehicle, the Hangzhou-headquartered car brand stated, must first undergo a strict “physical inspection” test that involves rigorous road testing and rain seal testing. Geely Auto takes advantage of its 2.4-kilometer test track to simulate 25 types of test road patterns such as twisting roads and highways that check performance, handling, mechanics, and electronics.
Only the vehicles that pass the track test can move on to the next stage, which involves a three-part rain seal test comprised of a 360-degree rain test, a three-minute rainstorm test, and a three-hour typhoon simulator.
Geely cars produced in Changxing
The cars produced in Geely’s Changxing factory include the fourth-generation Emgrand and Binray Cool sedans.
Also built here are two other project models under a joint venture with a German auto brand.
Photos from Juan Paulo Papa and Geely Auto
Also read:
Sell your car at the best price


-
Explore Geely Emgrand
Geely Car Models
Don't Miss
PIMS 2024
- Latest
- Popular
You might also be interested in
- News
- Featured Stories
- Upcoming
- Popular
Latest Geely Emgrand Car Videos on Zigwheels

Compare & Recommended
![]() |
![]() |
![]() |
![]() |
![]() |
Length
4638 mm
|
4601 mm
|
3995 mm
|
4475 mm
|
4420 mm
|
Width
1822 mm
|
1818 mm
|
1735 mm
|
1706 mm
|
1730 mm
|
Height
1460 mm
|
1489 mm
|
1515 mm
|
1469 mm
|
1475 mm
|
Power
102
|
112
|
82
|
89
|
98
|
Torque
142 Nm
|
150 Nm
|
113 Nm
|
132 Nm
|
123 Nm
|
Front Brake Type
Ventilated Discs
|
Ventilated Discs
|
Ventilated Discs
|
Ventilated Discs
|
Ventilated Discs
|
Rear Brake Type
Drums
|
Drums
|
Drums
|
Drums
|
Drums
|
Alloy Wheels
No
|
No
|
No
|
No
|
No
|
Headlamp Type
Projector Halogen
|
Halogen
|
Halogen
|
Halogen
|
Halogen
|
Centrally Mounted Fuel Tank
Yes
|
Yes
|
Yes
|
Yes
|
Yes
|
|
Trending Sedan
- Latest
- Upcoming
- Popular
Geely Emgrand Car Articles From Carmudi
- journal